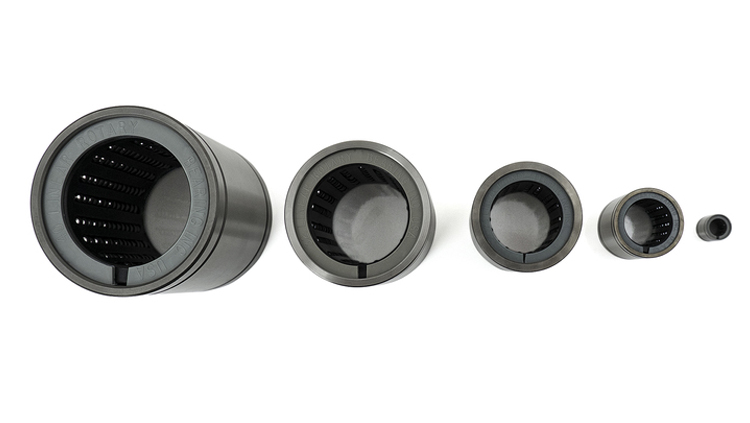
Specifications
SPECIFICATIONS
Linear Rotary Precision (LR) and Linear Rotary Super Precision (LRP)
Notes:
- The groove widths marked match standard retaining ring thicknesses.
- To order wipers - one end, add the suffix W, i.e. LR-W
- To order wipers - both ends, add the suffix WW, i.e. LR-WW
- For shaft to bearing selection a clearance of 0.0005 is recommended.
- Shaft diameters greater than specified could cause ball loss during insertion.
Chart 1 - Maximum Allowable Loads
Notes:
- Load ratings based on use with hardened shaft - Rockwell 60C.
- Based on travel life of 10 million inches.
- For speeds and loads not listed, consult Linear Rotary Bearings.
Chart 2 - Shaft Selection Chart
Standard AISI C-1060 Steel hardened to Rockwell 58/63C or 440C. Stainless steel shafts hardened to Rockwell 50/55C are charted below. Shafting can be supplied up to 12 feet long or can be cut to any length. Special tolerances, dimensions or end matching will be promptly quoted.
All units in inches, except where noted.
*For other sizes and tolerance, consult Linear Rotary Bearings.
Bearing Selection
Chart 3 - Load Correction Factor (Kl) vs. Travel Life in Millions of Inches
Chart 4 - Load Correction Factor (Kh) vs. Shaft Hardness - Rockwell "C"
Sizing Example
A pick and balance machine requires two linear rotary bearings. Total load is 800 lbs. Maximum rotation is 300 RPM. Shafts are to be hardened to Rc 55C. Travel life is required to be 25,000,000 inches.
Calculations:
Load bearing = 800 lbs / 2 = 400 lbs. @ 300 RPM
Shaft hardness RC 55: from Chart 4 we obtain a load correction factor Kh = 0.76
Load factor for 25,000,000 inches: from Chart 3 we obtain Kl = 0.75
Factored load capacity = 400 / (Kh * Kl) = 400 / (0.76 * 0.75) = 702 lbs.
From Chart 1, we obtain for 702 lbs. @ 300 RPM a Linear Rotary bearing rated at 878 lbs. (LR-40)
Calculate margin of safety = (878 / 702) - 1 = 25%
NOTE: Means of measuring inches of travel = Shaft diameter (inches) x 3.1416 x Revolutions + Linear Inches Travel
Shaft Selection
Because of its inherent geometric configuration, the linear rotary bearing has no inner race. Therefore, to take full advantage of its superior characteristics, proper shaft selection is mandatory. Under "Design Guidelines" correct diameters were suggested. To achieve the full rated life cycle and smooth operation, the shaft shoud be AISI C-1000 steel case hardened to Rockwell 58-63C or from 440 Stainless Steel, case hardened to Rockwell 50-55C. If shaft hardness cannot be met, see Chart 4 for the reduction factor.
Lubrication
The lubrication factor is a function of speed, linear plus rotary, where applicable. The faster the ball movement, the less viscous the oil required. It is theoretically possible to use no lubricant at high speeds. The load factor must also be considered. It is suggested that a light machine oil be used, if only to prevent corrosion.